Goal
More focus on activities that deliver observable value for the customer. Seeing waste and eliminating it or spending less time on it leaves more time for delivering customer value.
Why do we do things the way we do them? Often because we’ve always done them that way. People are creatures of habit. Nevertheless, it is good to look at our work from a different perspective. Understanding the eight forms of waste allows for greater focus on delivering value to the customer. By continuously addressing and eliminating waste, costs and process lead times decrease, while delivery reliability and quality increase.
- More feedback on collaboration
- Decrease in lead time
- More focus on delivering customer value
- Reduction in wasteful activities
Videos
Find the 8 forms of waste (4 minutes, EN)
See if you can spot examples of the 8 forms of waste from Lean.
Improved Process (2 minutes, EN)
See if you can spot the improvements in comparison to the first video.
To Work
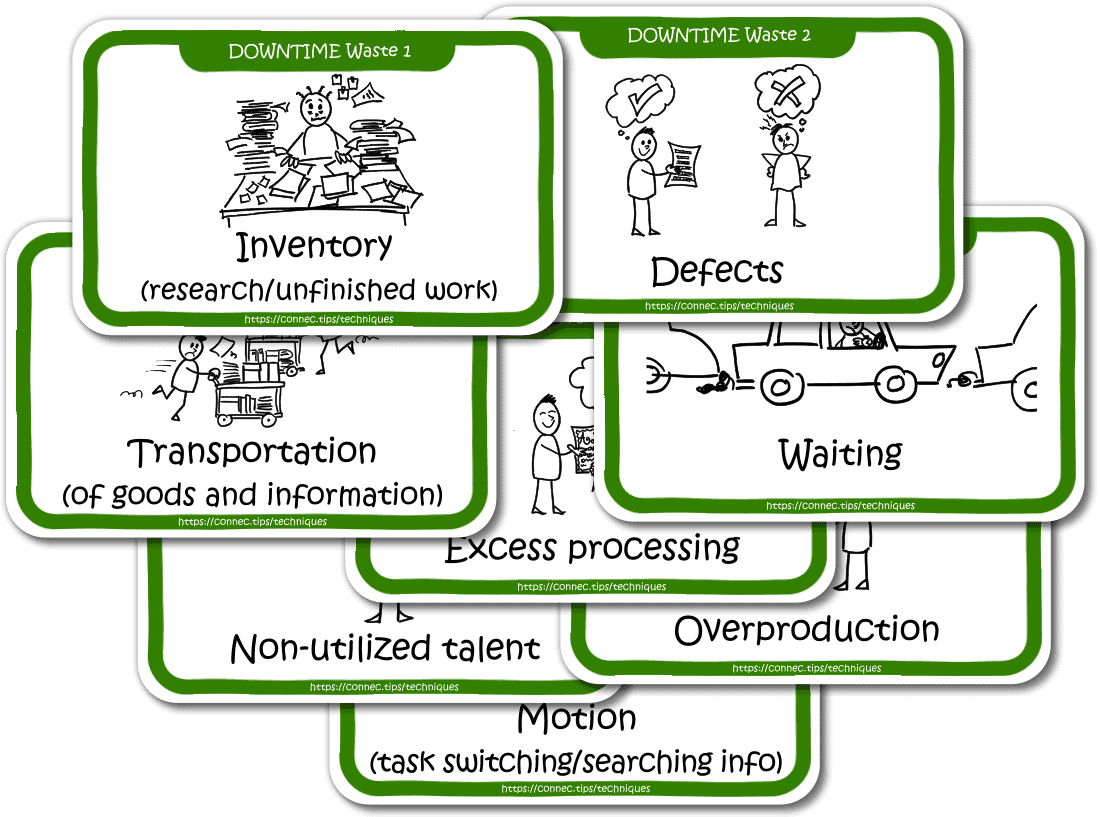
With your team or with a group of stakeholders, you work on reducing wasteful activities.
- Stick a card of a waste on a flip chart, read the explanation of this waste. Discuss common examples of this waste to get a common understanding of what the waste entails. Repeat this step for all 8 wastes.
- Jointly watch the video “Find the 8 forms of waste” above. Everyone silently writes down the wastes they recognize. This way you practice recognizing waste.
- Share the results with each other. Has everyone seen all the forms of waste? How do you recognize a waste? What do you learn from this for your team/organization? Then watch the “Improved Process” video above to see what you can do about these forms of waste.
- Take a few minutes of silence to individually writes examples of wasteful activities on a sticky notes (one per sticky note), which you recognize within your team/process/organization. Stick them to the relevant waste card.
- Stand at the overview of all examples of waste. Take turns to deduplicate the waste examples, ask for explanation, or group the ones that belong together. Keep taking turns until everyone is satisfied with the result.
- Use dot-voting to determine the priority/importance. For example, have everyone divide three dots. They may add multiple dots to one (group of) waste(s).
- Now choose which waste you as a team will deal with first. Devise concrete actions to combat these wastes. Select two or three actions from all the ideas that you will work on in the coming period.
Source
Fighting waste has its origins in the LEAN philosophy, derived from the Toyota Way of Working. The shortest definition of Lean is: ‘Developing employees so that they, collaboratively, eliminate waste.’ In this context, waste means all activities that cost unnecessary time or money and that the customer does not want to pay for.
You find a more detailed description of this technique in section 6.3 DOWNTIME Wastes in our book Connective Teamwork (EN, NL). The book helps you set your team in motion with a practical 5-step plan and 20 teamwork techniques.
You can learn more about and practice this technique in our Connective Team Coach Training Course.

Downloads
More resources
Contact me
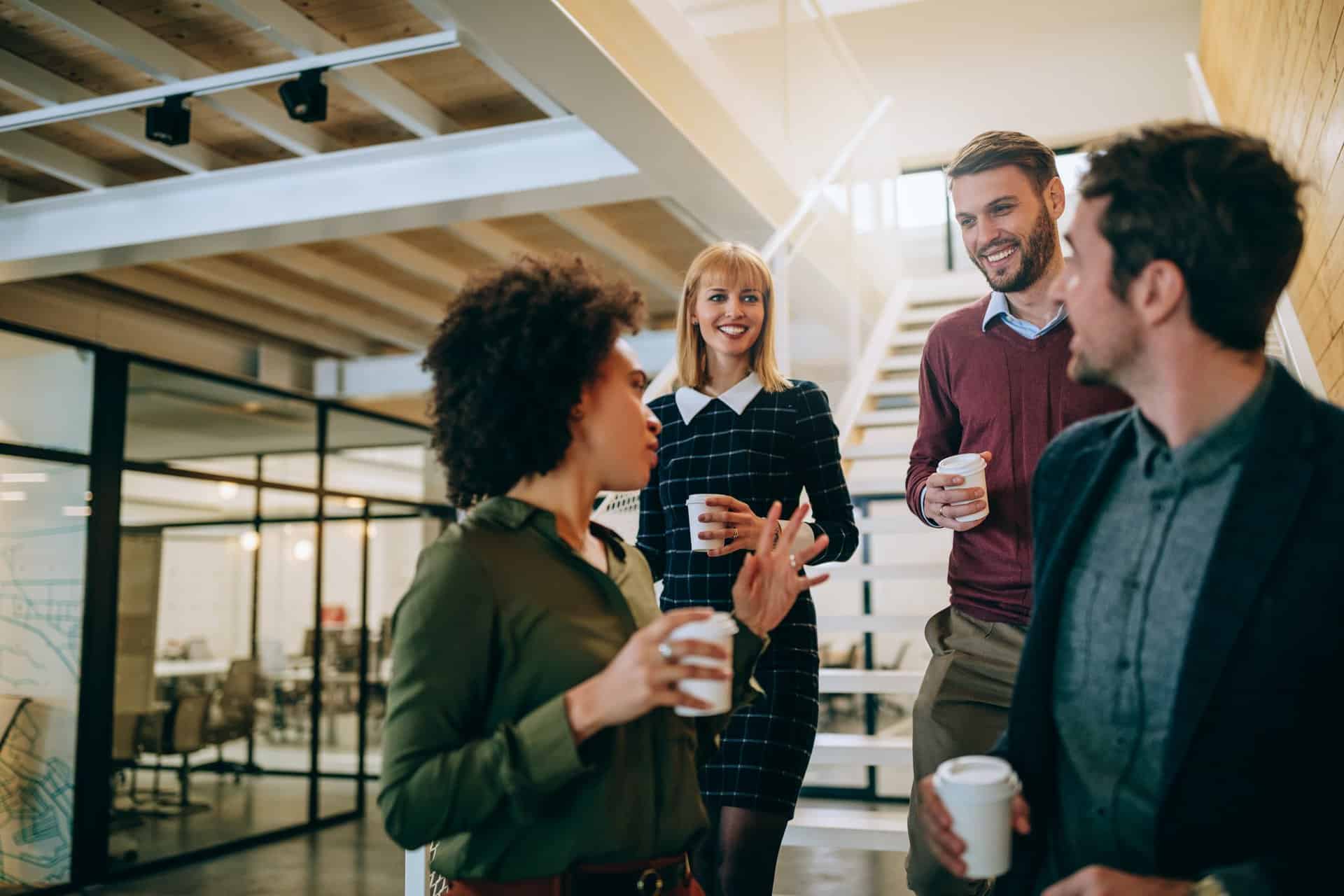